- Home
- Sustainability
- Quality Management
Relationships with Society
- Quality Management
- Procurement
- Human Resource, Diversity, Workplace
- Initiatives for Respecting Human Rights
- Health and productivity management
- Occupational Health and Safety, Disaster Prevention
- Contribution to Local Communities
Quality Management
Quality philosophy
We, the Dexerials Group, under our corporate vision of “Value Matters Unprecedented innovation, unprecedented value” contribute to our customer’s product value, through explore technologies, and provide high quality products and services.
Basic Policy
We challenge activities in all process of development, design, production and service to realize more attractive quality.
- 1.We provide safe and reliable products, and services.
- 2.We comply with relevant laws and regulations, agreement with customers, and internal standards surely.
- 3.We practice steadily implementing activities to reduce risks and preventive activities.
- 4.We improve professional standards and develop human resources by on the job training and education.
- 5.We ensure to utilize quality management system and improve effectiveness.
Quality promotion system
All of Dexerials Group’s manufacturing sites have obtained the international standard ISO9001 certification and our quality management systems (QMS) are the basis for business activities.
Moreover, in order to ensure compliance with laws and regulations and customer requirements, we have established a quality management system promotion framework led by top management, with chief administrator, division representatives, quality assurance heads, QMS promoters, etc.
Regarding products for automotive applications, we have obtained IATF16949 certification, a sector standard for the automotive industry.
We are working to ensure even stricter quality standards, including complying with the VDA standard, which is the quality standard of the German Association of the Automotive Industry.
Cross-organizational activities and cooperation are indispensable for achievement of quality targets and for realization of products. Each unit of activity that requires cooperation is designated as a business process, and is managed under a system of responsibility for each business process.
We also regularly conduct internal quality audits to monitor these activities. In these audits, internal quality auditors confirm whether business is conducted in accordance with legal regulations and rules, and whether on-site operations and manufacturing is performed in accordance with process and quality specifications.
Problems are then identified and improved upon and reported to top management. Because the skills of auditors are important in internal quality audits, we actively promote the accumulation of experience through mock audits and skill improvement training by trainers.
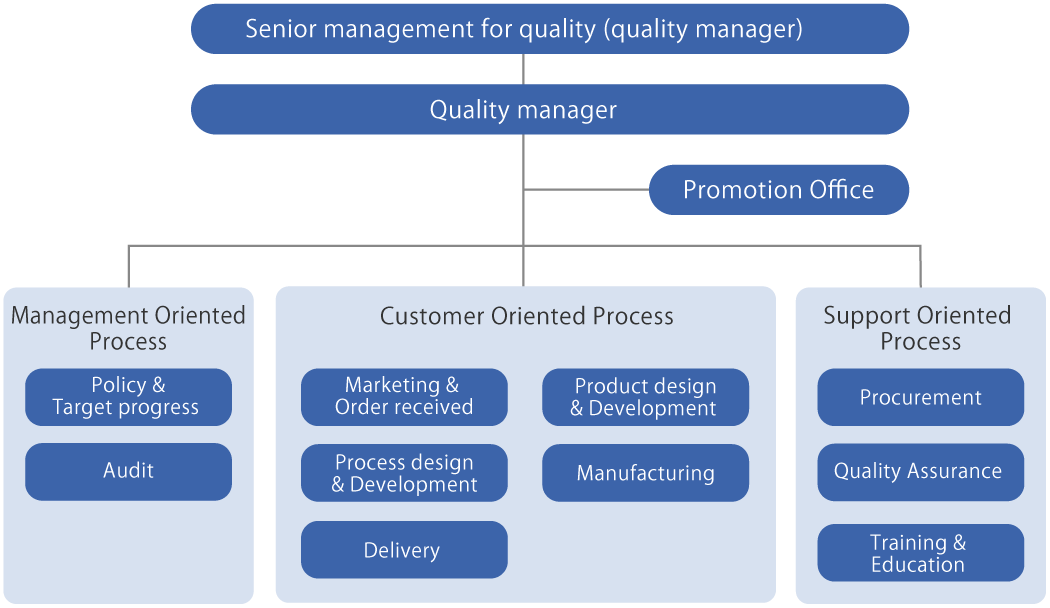
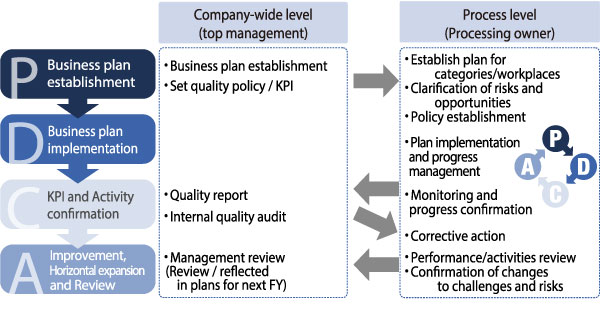
Acquisition status of quality management system certification
All the manufacturing sites of the Dexerials Group have obtained ISO 9001 certification for quality management systems that provide the basis for promotion of the quality philosophy and the basic policy and for business activities, such as design, development, manufacturing, and quality assurance.
Regarding products for automotive applications, we have obtained certification for IATF 16949, a standard for the automotive industry for the maintenance of the high quality and reliability required for automobile parts and we also comply with the VDA standard (quality standard of the German Association of the Automotive Industry).
ISO9001 Acquisition status of quality management system certification
Certification unit | Organization | Site |
---|---|---|
Dexerials Corporation | Dexerials Corporation | Headquarters and Tochigi Technology Center |
Kanuma Plant No.1 | ||
Kanuma Plant No.2 | ||
Tagajo Plant | ||
Tokyo Office | ||
Dexerials Photonics Solutions Corporation | Eniwa Operation | |
Kamisunagawa Operation | ||
Tome Operation | ||
Dexerials America Corporation | ||
Dexerials Europe B.V. | ||
Dexerials (Suzhou)Co.,Ltd. |
IATF16949 Automotive Quality Management System
Organization | Site |
---|---|
Dexerials Corporation | Kanuma Plant No.1 |
Kanuma Plant No.2 |
Product Safety
In line with our basic policy of making product safety the top priority, we test our products for compliance with a range of product safety standards and acquire the relevant certifications to ensure that products are safe for customers to use with complete confidence. Regarding the essential international standard, the UL standard (safety standards established by UL LCC, a company that enacts safety standards and conducts tests and certification), in particular, not only did we respond to the demand from customers for certification registration but also from the viewpoint of ensuring product safety, we have proactively received certification for various products in the Dexerials Group as we continue to supply safe products at the parts level.
As many of our products are in a liquid form, in order to accurately communicate product safety information to customers, Dexerials has introduced a dedicated system for preparation of safety data sheets (SDSs) and provides SDSs compliant with laws and regulations in Japan and abroad.
Promotion of DX (Digital Transformation) in quality control
The Dexerials Group is also promoting DX in quality control, believing the advanced data utilization (data driven) with cutting-edge technologies represented by AI, IoT, and data science, etc., will lead to its further growth.
We are working on increasing our competitiveness by innovatively improving quality based on the abundant data and knowledge which have been accumulated so far. Dexerials Group produces a lot of roll-shaped film products, which is its main product. As they are continuously produced over a long period of time, it has been a critical issue for quality control to prevent failures from occurring in series due to unexpected causes. In order to solve this problem, we are promoting efforts to establish a more sophisticated quality control system that can predict anomalies in advance and controls processes, and achieve a smart factory.
At the headquarters and Tochigi Technology Center, we incorporate the automated optical inspection equipment and auto measuring device using our proprietary image processing in antireflective films.
We have developed and built a system to classify defect images in real time and with high accuracy by utilizing the AI’s deep learning capabilities for the vast amount of data obtained from the equipment, and are moving forward with the development of smart factories.
These efforts have prevented the continuous occurrence of defects, reducing the defective product rate and significantly enhancing profitability. Moreover, we have further improved quality through the analysis of tens of thousands of pieces of data obtained during the production process. Furthermore, since fiscal 2022, we have been building a quality control system for preventative measures by linking data with SCADA* systems and other systems to improve the accuracy of anomaly detection and prediction. These smart factory developments are also being promoted at other sites.
- *SCADA: Supervisory Control And Data Acquisition system, integrated monitoring and control system that gathers on-site information in one place in the industrial field
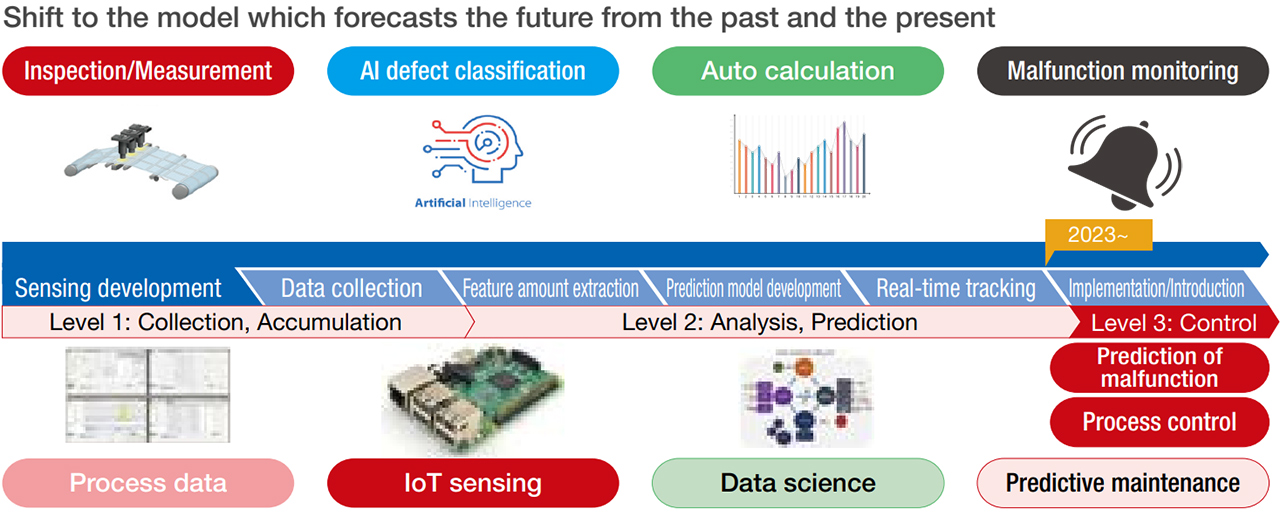
Quality Communication
Through communication with customers, the Dexerials Group shares customer needs and technology issues. We offer technology-based support and solutions, working toward the creation of products that respond to customers’ confidence in us and deliver customer satisfaction.
In the event of quality issues that could impact stakeholders, including where there is the threat of serious quality issues and product incidents occurring, a system is in place whereby the relevant corporate department promptly reports the situation to top management so that appropriate response measures can be taken.
Regarding returns and recoveries due to complaints made by customers, an analysis is performed by specialist technical staff with advanced analytical skills, and the analytical reports and follow-up measures are promptly implemented. For defects whose causes are difficult for customers to identify, we provide technical support for the investigation of the causes using our sophisticated analytical capabilities.
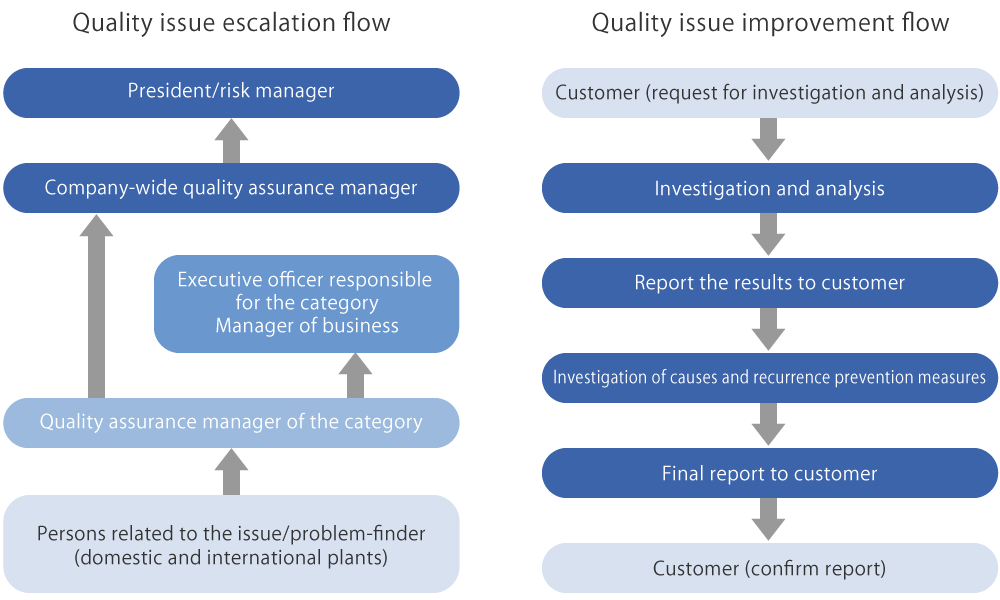
Technology Education and Human Resource Development
At Dexerials, based on our basic policy for human resource development with the objective of developing specialists, we are developing human resources who have excellent quality management capabilities.
We have produced a “roadmap for quality training” that clarifies the quality management knowledge required in each post in a wide range of levels, from new employees to specialized technicians. We also conduct training that covers practical exercises to help employees acquire basic and expert knowledge and tools for all divisions.
In response to changes in the educational environment due to the proliferation of remote work and the controlling of the spread of infectious diseases, we are striving to improve the convenience and efficiency of training and enhance educational opportunities by utilizing e-learning as the core training format and expanding the use of online training methods, shifting away from conventional group training methods.
In fiscal 2022, in addition to the existing e-learning courses such as the fundamentals of quality and ISO9001, and introduction to IATF16949, we are expanding the curriculum to include education on human error, corrective actions, and other topics.
In addition, to prevent corporate scandals related to quality, which has been an issue in recent years, we provide training for all employees every fiscal year that includes compliance related to quality and corporate ethics as a basis for correct judgment and actions.
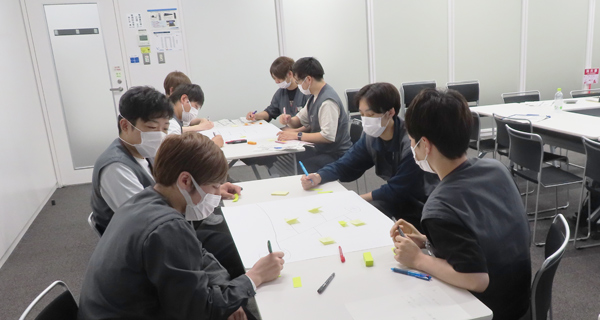
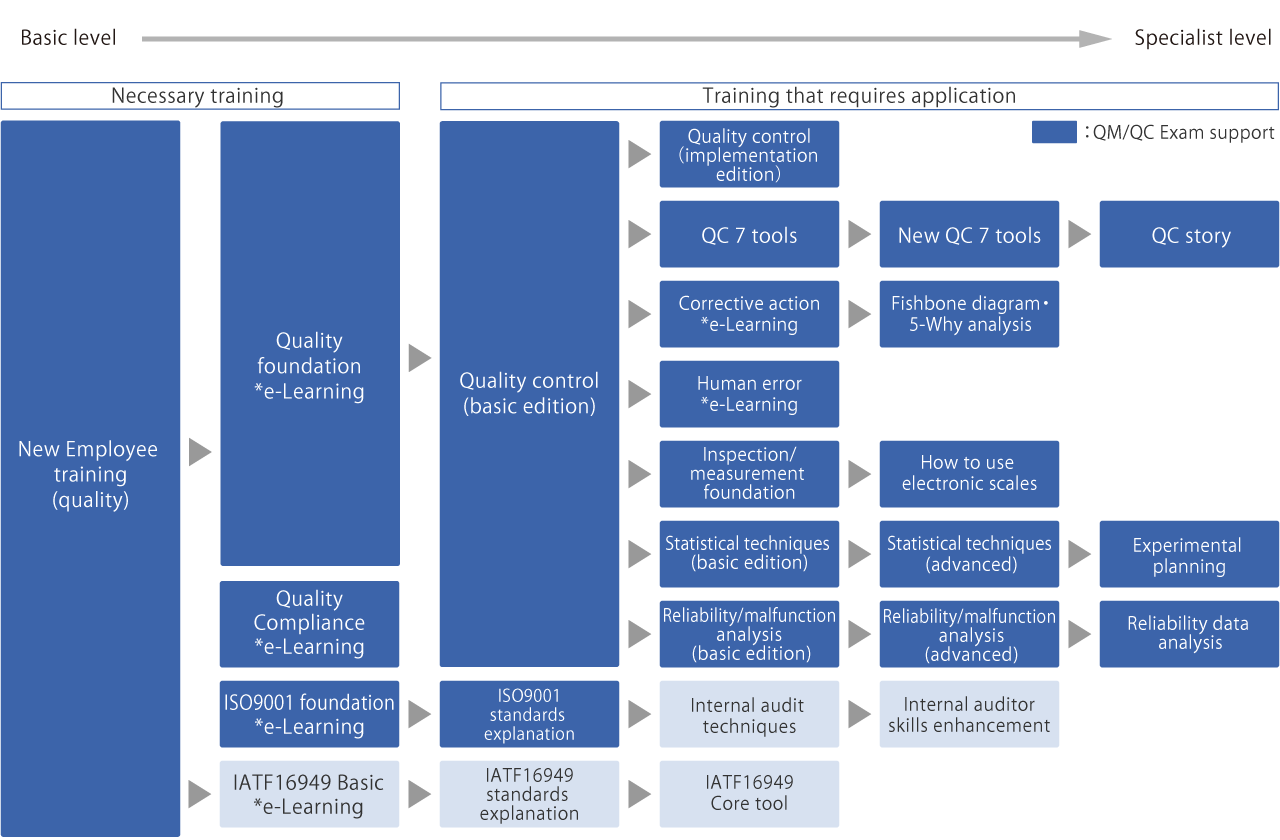