ACF(異方性導電膜)による実装プロセスの生産性を飛躍的に向上させる 新工法「ACF一括圧着接続工法」および材料を開発・実用化
新製品
2006.08.03
この度、ソニーケミカル&インフォメーションデバイス株式会社(以下、ソニーケミカル&インフォメーションデバイス)では、今まで難しいと考えられていたACF(異方性導電膜)による多チップ一括圧着接続を可能とする、新しい工法および、その実装工法に対応した専用ACFを開発いたしました。 この新ACF実装プロセスおよび専用ACFにより生産性を飛躍的に向上することを可能としました。
新実装工法開発背景
特殊用途工法から一般用途工法へ。ソニーケミカル&インフォメーションデバイスの挑戦。
1996年、ソニーケミカル株式会社(当時)がCSP(Chip Size Package)用のACFを世界で初めて上市して以来、「多接点を一括で実装できる」、「ファインピッチ化が可能」、「軽薄短小化が可能」といった各種メリットが注目され、実装プロセスへの活用の可能性が広く検討されてきました。また現在では、50μm以下の電極ピッチでも充分に接合できるというACFの特長が高く評価され、コントロール系やメモリー系など一部の半導体実装分野に採用され、ACFを使ったLSI実装によるパッケージ生産に採用されています。
しかし、ACFは半導体パッケージ市場において一般的な工法として採用されているわけではありません。それは、LSIを実装する際の生産性に課題があったからです。今までのACF工法による半導体実装ではチップとサブスレートを傾きなく加圧する必要があり、1チップごとに精密な調整を行いながら圧着しなければなりませんでした。さらに、1チップの実装に20秒程度の圧着硬化時間を必要とするため、生産数量を上げるには多くの設備を必要とする問題もありました。今回発表する新工法および専用ACFはこうした課題を解決し、半導体パッケージ市場でのACF実装工法の裾野を広げる新工法として開発いたしました。
新実装工法及び専用ACFの特長
特長1: 大量のチップを一括加圧。1チップ当たりの圧着時間を数十分の一に大幅圧縮。
今回、ソニーケミカル&インフォメーションデバイスが開発した新工法の最大の特長は、1チップ当たりの圧着時間を数十分の一に短縮し、実装プロセスの生産性を大幅に向上できることにあります。この工法は、熱圧着機に新開発の特殊なツールを装着することにより、集合基板上に仮搭載された数10個のチップを一括加圧・実装を可能とするものです。この新工法により、例えば40チップを20秒で一括圧着すれば、1チップ当たりの生産タクトは0.5秒以下と飛躍的に向上し、生産リードタイムの短縮に大きく貢献します。
特長2: 膨大な設備投資をすることなく、生産性の大幅アップを実現。
さらに、この設備自体は複雑な構造を必要としないため、大きな設備投資を必要としないことも特長です。 多チップを一括でACF圧着するという工法はこれまでもいろいろ検討されてきましたが、従来の圧着機で多チップを一括圧着すると、どうしても個々のチップの平行度を保つことが難しく実用化には至っていませんでした。 今回ソニーケミカル&インフォメーションデバイスが開発した新工法はこの問題を解消し、より簡単な構造ですべてのチップを均一かつ高精度に加圧実装できます。このことにより、精度を必要とする平行度調整の手間もなくなり、大幅な生産性の向上が可能となります。【※写真1】
特長3: 微少なボイドを排除し、パッケージの信頼性を向上
また、この新工法専用に開発されたACFを組み合わせることにより、これまでの工法ではどうしても排除できなかった、チップとサブスレート間の微少なボイドまで排除でき、パッケージの信頼性を格段に向上することが可能となります。 さらに、フィレットと呼ばれるチップ周りの樹脂形状【※写真2】も、気泡【※写真3】を巻き込むことなくキレイな形状に仕上げられることも新たな利点です。
特長4: RoHS指令に準拠した、環境対応工法。
もちろん、ACF圧着による半導体パッケージは鉛を含有していないため、RoHS指令への対応も容易で環境に負担をかけることなく、安心してご利用いただけます。
半導体パッケージ実装の生産性向上に大きく寄与するこの新工法と専用ACFの開発により、ACFによる半導体パッケージ技術の実装工法として一般的に普及するものと、ソニーケミカル&インフォメーションデバイスでは考えております。
- ACF一括圧着接続工法 -


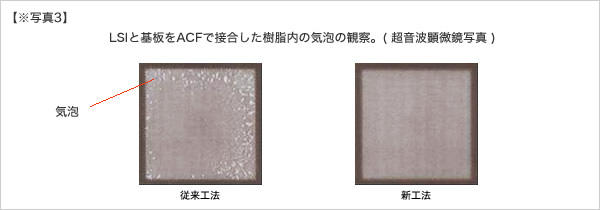