- Home
- Research & Development
- Overview of Dexerials Technologies
- Process technology
Process technology
Dexerials owns a wide range of technologies used to build production processes for making functional materials. For example, organic material technology to mix/disperse/synthesize materials, inorganic technology for crystal growth, technology to coat thin materials on base film or forming thin layers in vacuum environment, and technology to cut films into required shapes.
Many engineers with expertise in mechanics, electronics and controlling system are engaging on the development of new manufacturing processes that can be utilized in customer’s products, which are becoming downsizing and high performance.
Microstructure formation technology
Nano- to micro-scale fine structures are formed on planar substrates and curved-surface substrates
We use the lithography technology used typically in the semiconductor industry to fabricate nano- to micrometer-scale fine structures. One of our strengths is that we can fabricate such fine structures both on planar substrates and on curved-surface substrates. The technology for the former process was applied to optical devices such as inorganic polarizers whose sales started in 2008, and the latter process was used in the technology that fabricates fine structures continuously on a roll film with a length of 4,000 meters. These applied products are marketed to various industries.
Many engineers with expertise in physics, electronics and mechanical systems are involved in development of nanostructures and microstructures by working together with our chemical engineers to realize functions required by our customers.
We will introduce some of the examples of high performance manufacturing by our technology to address market trends and issues, and other applications.
Microlens fabricating technology
Compared to conventional light sources, lasers have better power efficiency and is friendlier for the environment. Thus, we can see more lasers used as light source for optical devices such as projectors.
However due to the directionality of laser, the beam need to be diffused to function as a light source. Diffuser, which spreads the laser beam at a required angle in uniform brightness, becomes necessary.
With the use of our micro-lens fabrication technology we have successfully commercialized an extremely reliable diffuser with ideal diffusion characteristics.
This technology, which we have developed over the span of many years, can create very accurate lens shapes on an inorganic material such as glass or quartz.
Examples of products using this technology
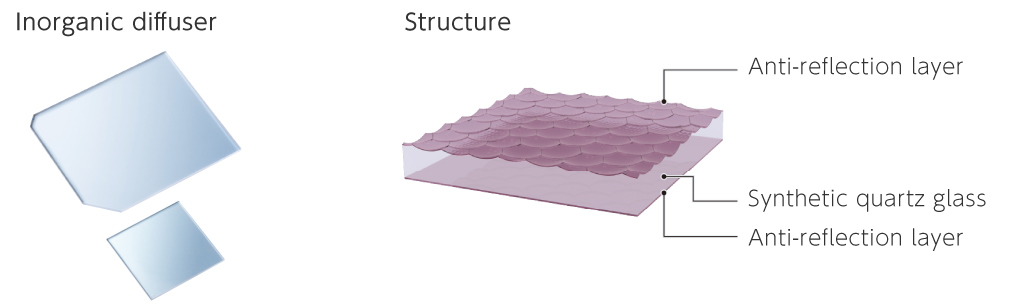
Fine structure fabricating technology using the roll-to-roll imprint process
Over many years, we have carried out R&D of the roll-to-roll imprint technology, which is a process technology to form nano- to micro-scale fine structures continuously, and then has established the key technology of fine-processing a cylindrical master and the roll-to-roll imprint technology that uses this master. We use these technologies to fabricate fine structures continuously on base films and manufacture highly transparent and excellent anti-reflection films in large quantities.
Examples of products using this technology
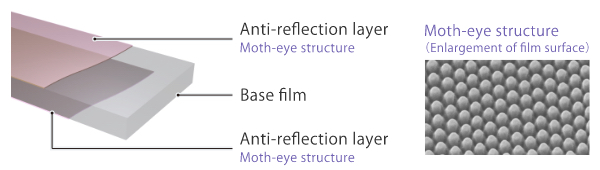
"Fine structure fabricating technology on cylindrical master" is a technique to engrave fine patterns on cylindrical master using precision machining or lithography. A variety of structures can be produced, ranging from nanosized moth-eye shapes to microsized reflectors, diffusers and micro-lens arrays.
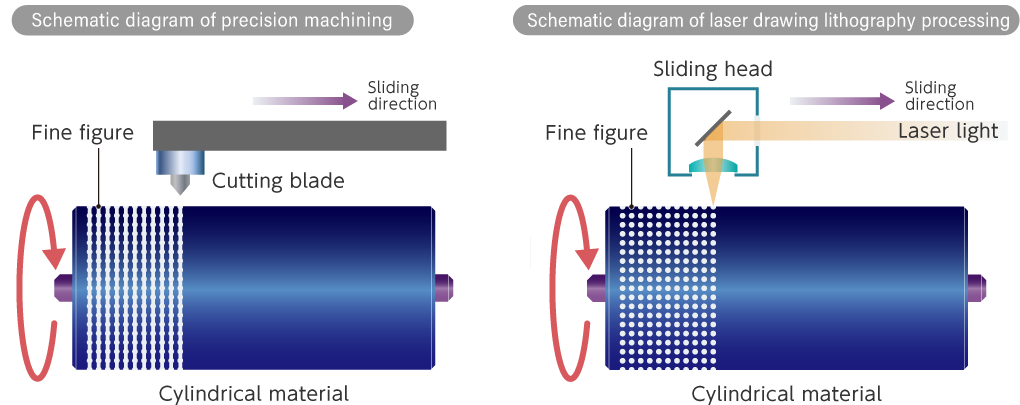
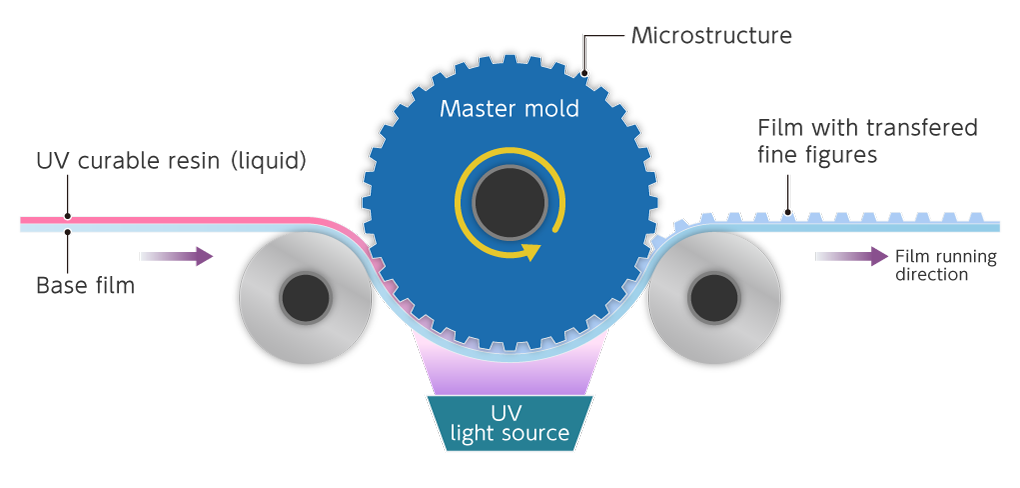
●This figure shows the process of continuous pattern fabrication onto a roll base film (roll-to-roll process).
Base film moves from left to right. After applying UV curable resin on the surface of the base film, cylindrical master engraved with micro (nano) pattern is pressed against the base film (and UV resin). When UV light is exposed, patterns on master will be transferred to the roll film.
The shape of the pattern transferred to the base film is an inversion of the pattern made on the master.