- Home
- Sustainability
- Initiatives to reduce environmental impact
Initiatives to reduce environmental impact
Reducing CO2 emission volumes~Dealing with climate change~
Dexerials Photonics Solutions Corporation purchased carbon offsetting forest absorption credit (J-VER) for forests owned by Tome City
Dexerials Photonics Solutions Corporation, a consolidated subsidiary of Dexerials, purchased a part of the carbon offsetting credit (J-VER), i.e., the absorption volume of CO2 emissions, Tome City, Miyagi Prefecture was granted from the Ministry of the Environment by tree thinning in the city-owned forest. We purchased the credit equivalent to 100 t-CO2 with a view to offsetting our emissions in the future.
Use of total heat exchangers for air conditioning systems(Tochigi Technology Center)
We investigated reducing energy usage in air conditioning systems when constructing the floor of the No. 4 building at the Tochigi Technology Center. With conventional outside air exchange, heating was required by means of a heater for air temperature control in winter in particular. By introducing total heat exchangers, the temperature difference in comparison to outside air during ventilation can be eliminated and heating by means of heaters becomes unnecessary, which enables an annual reduction in energy of 200,000 kWh (97 t-CO2).
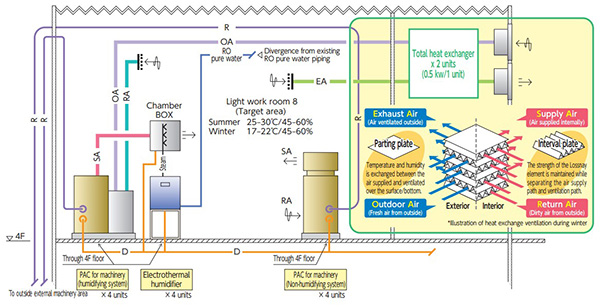
Cooperation with heat source central monitoring system and management strengthening(Kanuma Plant No.2)
At Kanuma Plant No.2, various types of equipment on the premises are being managed by means of heat source central monitoring. This includes turbo freezers that supply cool water to air conditioners, but there was a loss of energy during low-temperature seasons as temperature settings have been fixed for the entire year. By means of cooperation with central monitoring systems, outside air temperatures are being monitored and managed, which enables the temperature to be controlled according to the outside air temperature rather by means of year-round set temperatures, thereby achieving an improvement in COP*2 and an annual reduction in energy of 68,000 kWh (33 t-CO2).
Fluorocarbon emissions reduction countermeasure(All Plants)
We are carrying out activities so that fluorocarbon is not emitted, such as attaching the “machinery using fluorocarbon” management label to machinery that uses fluorocarbon, which visualizes fluorocarbon use and controls simple checks, regular inspections and disposal, etc.
Reducing power consumption by introducing of inverters in deodorizing equipment (Kanuma Plant)
At the Kanuma Plant, because many organic solvents are used in the process of mixing of liquid adhesive agents, it is necessary to use deodorizing equipment to extract exhaust gases which contain organic solvents. Conventional deodorizing equipment is operated on a 24-hour basis. However, in consideration of energy-saving, we introduced an inverter for the electric motor so as to operate the equipment according to the emission of organic solvents. This achieved a total energy reduction of 198,000 kWh (72 t-CO2) per year.
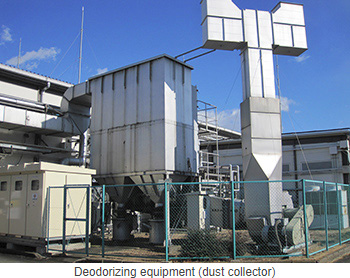
Reducing power consumption by introducing high energy-saving models (Dexerials (Suzhou) Co., Ltd)
When establishing a new plant, Dexerials (Suzhou) Co., Ltd. introduced high-efficiency, inverter-controlled chillers and air-handling units (AHU). This introduction has resulted in energy savings of about 500,000 kWh (377 t-CO2) per year compared with existing equipment in the plant.
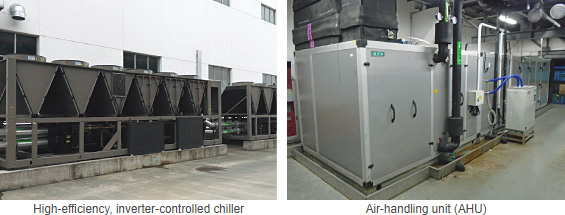
Reducing power consumption accompanied by replacement of packaged air conditioners (Kanuma Plant)
The laboratories for optical films and optical elastic resin (SVR) were air conditioned with three floor-installation-type large-sized packaged air conditioners; however, the laboratories could not be appropriately air conditioned because air blown out from the conditioners did not spread over the entire space occupied by the laboratories. Two floor-installation-type large-sized packaged air conditioners were replaced with five ceiling-suspension-type small-sized packaged air conditioners, allowing minute and appropriate air conditioning of the entire space occupied by the laboratories. This has resulted in energy savings equivalent to 40,000 kWh (electricity) (15 t-CO2) per year.
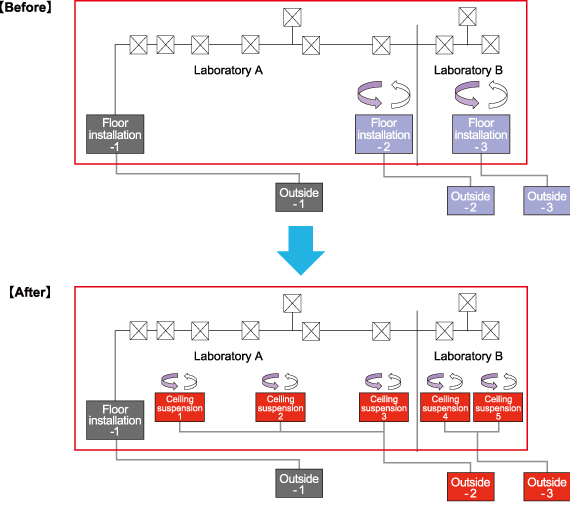
Reducing power consumption by introducing inverter coolant pumps (Kanuma Plant)
Cooling water pumps for absorption chillers, which operated using a certain volume of water, provided cooling water for air conditioners used in the process of producing Anisotropic Conductive Film (ACF) and industrial adhesive tapes. The pumps were replaced with inverter coolant pumps. The purpose of this was to establish a cooling system most appropriate for controlling the cooling water flow of the inverter pumps based on operation data of each chiller. This has resulted in energy savings equivalent to 140,000 kWh (electricity) (53 t-CO2) per year.
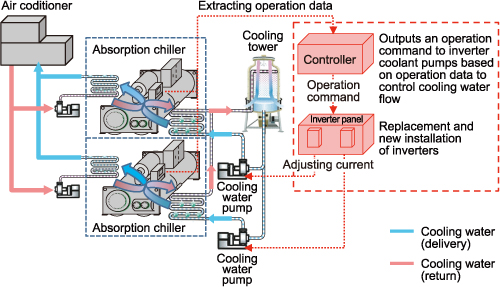
Reducing power consumption and gas emissions of air conditioners through the circulation of air conditioning in explosion-proof areas (Kanuma Plant)
Explosion-proof areas where battery components are produced were air conditioned through the intake and exhaust of the total amount of air; that is, 100% air in the areas was exhausted and 100% outside air was drawn in. Accompanied by the change of products to be manufactured, air conditioning and exhaust equipment were reviewed and consultations were held with the Kanuma City Fire Department to check safety. Based on the review and consultations, air conditioned air is now circulated. This has resulted in energy savings equivalent to 173,000 kWh (electricity) (65 t-CO2) and 75,000 m3 (city gas) (158 t-CO2) per year.
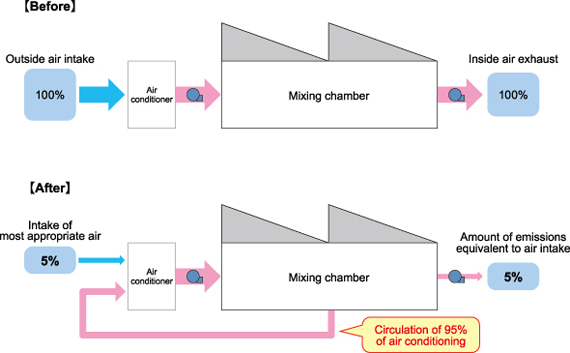
Reducing power consumption by reviewing operation of air-conditioning equipment in the clean room on days off (Kanuma Plant)
In the clean room where Anisotropic Conductive Film (ACF) is produced, air-conditioning equipment operates continuously throughout the year to maintain cleanliness in the room. To reduce power consumption, operation of the equipment on days off when the Kanuma Plant is not in operation was reviewed. As a result of the review, air intake and amount of emissions have been adjusted while operating an inside air-processing unit to maintain cleanliness in the clean room, decreasing the operating power of an outside air-processing unit that uses a lot of electricity to keep air at an appropriate temperature. This has resulted in energy savings of 1.08 million kWh (408 t-CO2 reduction) per year.
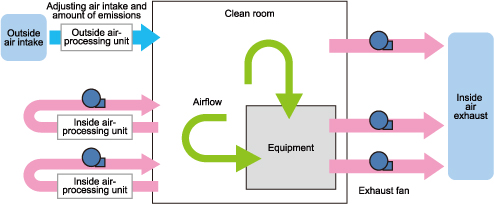
Reducing the energy cost for air conditioning (Dexerials Photonics Solutions Corporation and Dexerials (Suzhou) Co., Ltd)
At Dexerials Photonics Solutions Corporation, the operating time of air conditioning facilities during the non-operating hours of the plant was changed after studying the potential impact on product quality and manufacturing equipment and confirming that there will be no problems. As a result, energy was reduced by 200,000 kWh (76t-CO2) in a year.
Similar measures were taken abroad as well. Dexerials (Suzhou) Co., Ltd. reduced energy by 1,140,000 kWh (858t-CO2) in a year.
Reducing power consumption and gas emissions through the tuning for energy-saving for the deodorization system (Kanuma Plant)
Power Consumption and gas emissions were reduced by applying the tuning measure for energy-saving to the deodorization system that treats organic solvent emission.
Since the equipment was installed, it had been operated based on the design condition that assumes the peak load. Through the tuning for energy-saving, the temperature-regulated pressure rising operation was discontinued, the stand-by operation time was abolished, and the temperature to stop maintaining the heat and the temperature setting for combustion were re-examined. Through these measures, energy was reduced by 20,000 kWh (electricity) (8t-CO2) and by 55,000 m3 (gas) (116t-CO2) in a year.
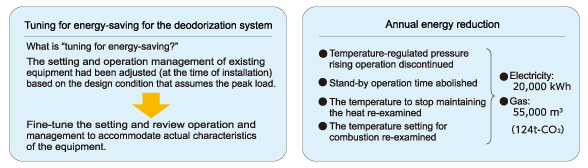
Reducing power consumption and gas emissions of air conditioners through an energy-saving measure based on analysis and improvement (Kanuma Plant)
A new energy-saving measure based on “analysis and improvement” was used. Under this measure, the use of energy is analyzed and waste is cut. By using this measure to re-examine the system of freeze prevention control for air conditioners, energy was reduced by 60,000 kWh (electricity) (23t-CO2) and by 43,000 m3 (gas) (91t-CO2) in a year.
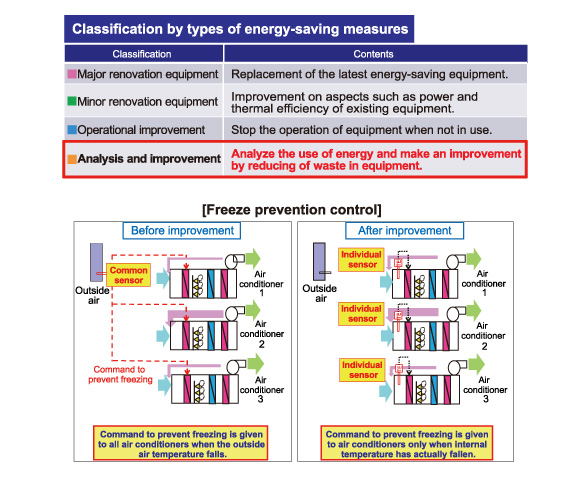
Reducing power consumption by prioritizing the operation of chillers with high energy-saving effect (Kanuma Plant)
Previously, two inverter-controlled chillers and two constant-speed chillers were operated in accordance with the load. However, reduction of 590,000 kWh (223t-CO2) was achieved in a year by prioritizing the operation of inverter-controlled chillers with high energy-saving effect.
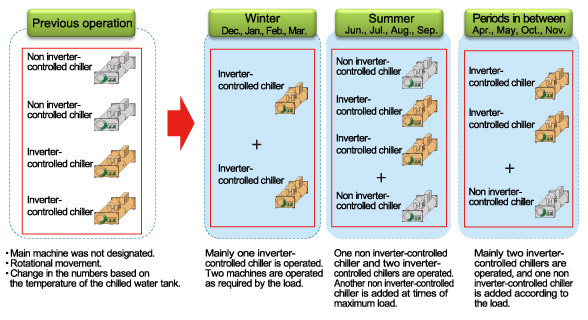
Reducing power by using plug fan air conditioners (Kanuma Plant)
Air conditioners consume a vast amount of energy, so they are a key focus of energy conservation measures. Switching from conventional belt-driven sirrocco fans to plug fans, which do not use a fan belt and reduce belt transmission loss by being directly coupled to the fan shaft, led to 31,000 kWh per fan of energy being conserved annually, in terms of air conditioning power.
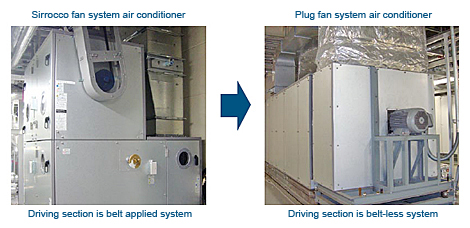
Reducing power by spraying water on air-cooled chillers (Kanuma Plant)
Condensing pressure has been reduced and the efficiency of energy consumption during cooling substantially increased by spraying water onto the air heat exchangers (condensers), in order to improve the cooling capabilities of air-cooled heat pumps. Repeated tests of nozzle angle, number, and spray volume were carried out when installing the spray nozzles, with a view to improving COP* leading to 23,000 kWh of energy being conserved annually.
* COP = Coefficient of performance
A coefficient used as a guide to the energy consumption efficiency of cooling equipment. The figure expresses cooling/heating capabilities per kW of electricity consumed.
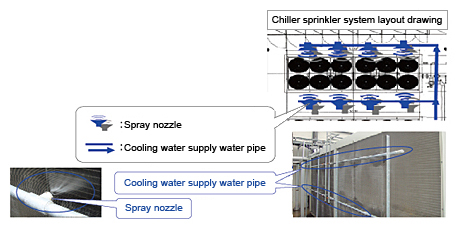
Reducing the drive power of cooling water pumps used in refrigerating machines (Kanuma Plant)
The cooling water pumps used in turbo refrigerating machines operate using a certain volume of cooling water, regardless of outside air temperature or humidity, so they were particularly inefficient during intermediate seasons and winter, when there was little air conditioning load. Controlling the volume of cooling water and automatically setting the optimum cooling water temperature (summer / intermediate seasons / winter) using an inverter (INV) that responds to the constantly-changing wet-bulb temperature has led to the conservation of 170,000 kWh of energy annually.
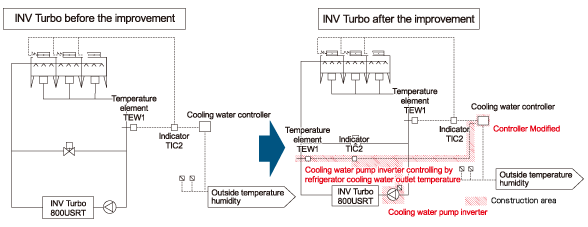
Strengthen the activities of energy conservation in the workplaces (All Plants)
To strengthen the activities of energy conservation in the workplaces, we are promoting visible conservation activities such as strict control of room temperature for air-conditioning system as approach to "Cool Biz & Warm Biz" and removal of fluorescent lighting from vending machines.
CO2 emissions have been reduced by changing the fuel for boilers and the deodorization system (Voc oxidizers) from heavy oil to LNG and by introducing (centrifugal liquid chiller). (Kanuma Plant)
At Kanuma Plant, CO2 emissions and energy consumption (energy costs) have been reduced by 20% (CO2 reductions: 12,100t-CO2/year) by changing the fuel for the boilers and deodorization system (heavy oil) to LNG and by introducing an efficient turbo refrigerator.
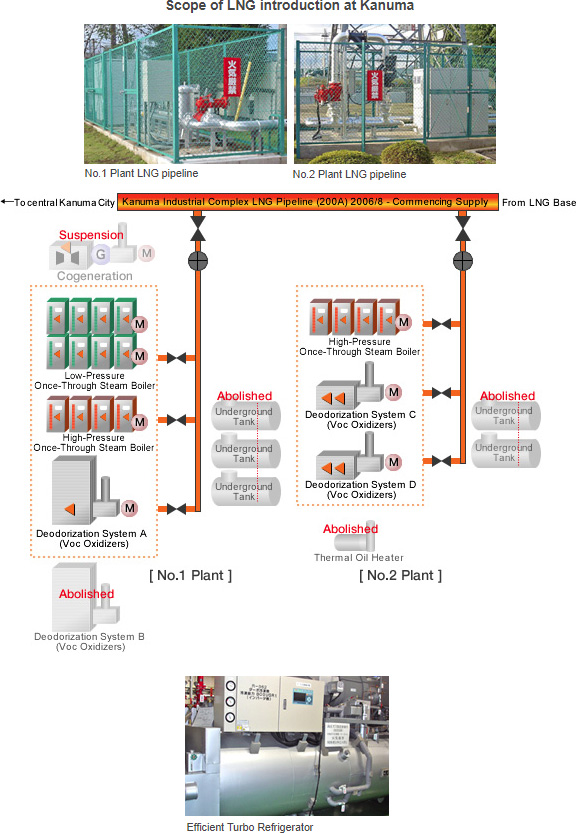
Reduction of water usage
Reducing the volume of pure water used (Dexerials Photonics Solutions Corporation)
At the Dexerials Photonics Solutions Corporation, the burden on the environment is being reduced by switching from a cleaning process that used chemical substances to a process that uses pure water, and proactive efforts are also being made to reduce the overall volume of pure water used.
The manufacturing division is implementing process improvements, including switching from central control tanks to single control tanks for processes involving a large amount of pollutants, thereby reducing the frequency with which the water in the central control tank needs to be replaced. In addition, it has investigated the optimum flow rate for cleaning equipment and is reducing running times.
Moreover, five pure water manufacturing units were conventionally used to supply the pure water used by 18 items of equipment, but the flow rate of pure water was optimized at a level that was satisfactory in terms of process quality, enabling the plant to achieve a 16% reduction in the volume of water used. Subsequently, in the pursuit of even more effective reduction measures, plant staff turned their attention to blow water from the pure water manufacturing units: by consolidating the three pure water supply lines into two and stopping the other, they were able to verify the burden on the pure water manufacturing units and the stoppage patterns, thereby curbing running costs and reducing the volume of pure water used. Moreover, halting use of one (5 t) of the five pure water manufacturing units has reduced electricity usage.
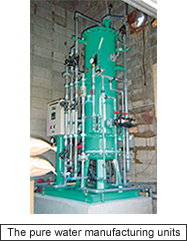
Reduction of industrial waste
Reuse
Reducing Waste Drums (Kanuma Plant)
Kanuma Plant keeps approximately 500 drums per month at all times. In FY2013, focus was given to the effective use of drums that were used when raw materials were purchased. As a result, drums with stains (3,100 drums per year), which used to be disposed, were used instead for discarding industrial waste, and new purchases from outside, which used to be 660 drums per year, reached zero, as the used drums were interchanged within the whole plant.
Introduction of reusable shipping cartons (Dexerials (Suzhou) Co., Ltd.)
Dexerials (Suzhou) has changed over from the cardboard boxes previously used to plastic shipping boxes that can be used for 12 months. A single model enables reduction of 10 tons of waste a year. Moreover, the previous vinyl wrapping has been changed to special securing bands, resulting in a reduction in the amount of vinyl wrapping used.
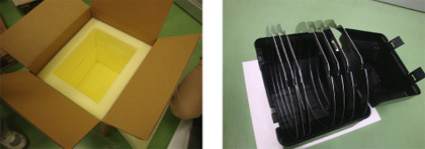
Changing from the previous cardboard boxes to plastic shipping cartons that can be used for 12 months resulted in an annual reduction in waste of 10 tons per model. While the previous method of securing reusable shipping cartons with vinyl wrapping produced large volumes of scrap plastic, the process was improved by securing cartons with bands, promoting activities to reduce vinyl wrapping.
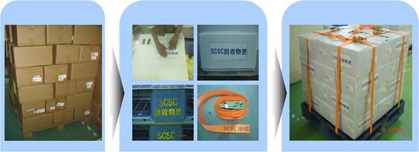
Reducing packing materials through the introduction of returnable containers (All Domestic Plants)
At all domestic plants, products for domestic distribution were loaded onto palettes and had their corner and wrapping materials further reinforced before being shipped. However, although these packing materials were either completely recycled (valuable materials) or disposed of as industrial waste after being shipped, these represented wasteful parts with no added value from the perspective of the product. Therefore, in October 2008 we established a shipping system using returnable containers, thereby achieving a substantial reduction in our packing materials.
Processing and recycling non-standard products for different applications (Kanuma Plant)
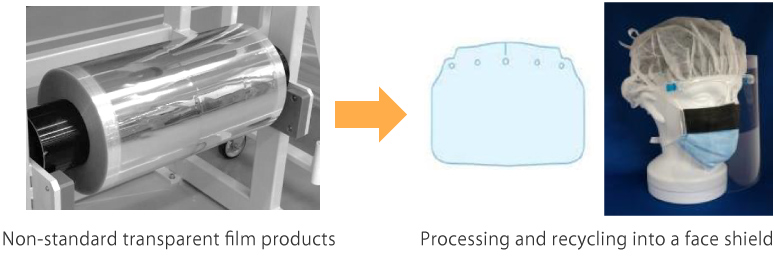
Recycling
Dexerials took a stake in R Plus Japan, Ltd.
Dexerials took a stake in R Plus Japan, Ltd. in support of its corporate spirit. R Plus Japan operates a business to recycle used plastics. Going forward, we will contribute to reducing environmental burden and realizing a sustainable society through resources recycling using R Plus Japan’s chemical recycling technique.
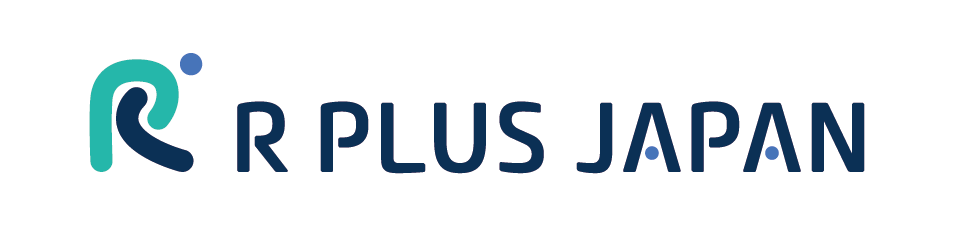
Effective use of resources through RPF recycling (converting waste to solid fuel) (All Domestic Plants and Dexerials (Suzhou) Co., Ltd.)
At all domestic plants, as well as at Dexerials (Suzhou) Co., Ltd., plastic film offcuts from production processes have always been treated as valuable resources. Those that have other materials (mainly adhesives) stuck to them as a result of the production process, which cannot be treated as valuable resources, are disposed of as industrial waste and used effectively as a resource through RPF* recycling.
- *RPF (Refuse Paper & Plastic Fuel) : Solid fuel of a high calorie which is made from used paper and a plastic with difficult material recycle as materials with industrial system waste.
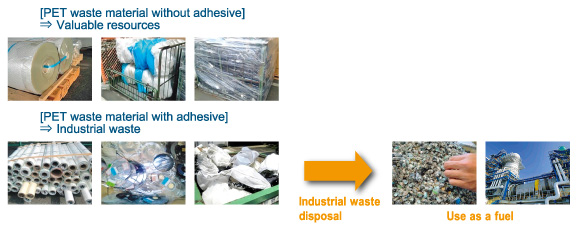
Promoting Recycling Month (Dexerials Photonics Solutions Corporation)
Promoting October 20 as Recycling Day
The "Sort burnable waste. Increase recyclable waste," campaign was implemented.
Reduction
Reducing Organic Solvents in the Manufacturing Process of Liquid Adhesives (Kanuma Plant)
Kanuma Plant deals with a large amount of organic solvents. It is working on improvements focusing not only on the reduction of their use, but also on the reduction of their emissions.
Measures taken to reduce environmental load by reducing organic solvents included: (1) reducing volatilization of organic solvents from cleaning tanks; and (2) reuse of cleaning solvents. As a result, the use of organic solvents was reduced by 16.5 tons per year, and waste disposal was reduced by 5.8 tons per year.
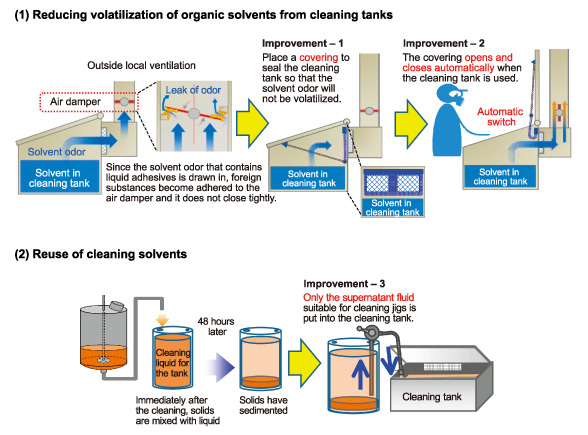
Activities to reduce food waste (All Domestic Plants)
The Dexerials Group is promoting activities aimed at reducing food waste (leftovers) from its staff canteens. Ongoing activities are being undertaken in partnership with canteen contractors, with measures including the use of displays of sample menus, confirming the number of employees in order to prevent too many meals being made, and thorough draining of leftovers.
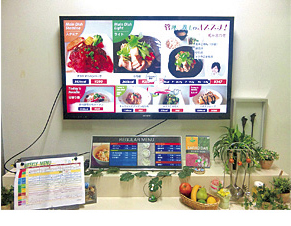
VOC emissions volume reduction
Reducing VOC via a system for treating exhaust gas containing organic solvents (Kanuma Plant)
At the Kanuma Plant, a direct combustion deodorizer that carried out pyrolysis of odors was formerly used to prevent the VOC generated during the manufacturing process from being discharged into the air, but in 1999 the plant became the first in the industry to introduce a heat storage deodorizer, in order to reduce the quantity of heavy oil used.
Furthermore, in 2006 it switched from using heavy oil to natural gas as a fuel, reducing the annual volume of CO2 emissions by about 30%.
Ceramics are packed at the mouth of the burner and the device uses self-energy from the gaseous solvent for combustion, providing a high heat recovery effect.
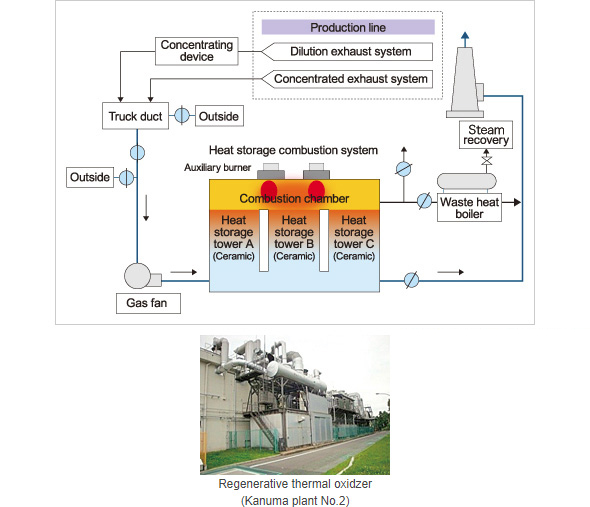